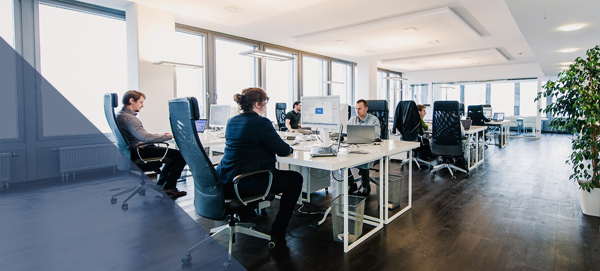
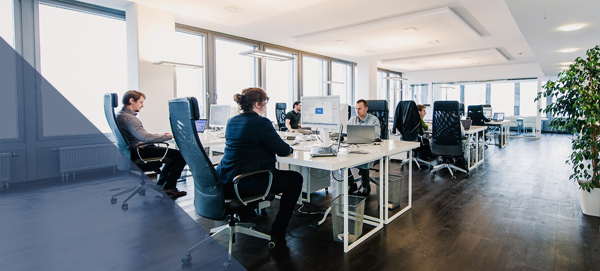
Aluminum Extrusion With its experience and know-how in the production of profile, Aydınoğlu Aluminum always produces quality products in line with your needs with the most reasonable price guarantee and sends you analysis reports..
Button TextAluminum extrusion is the definition of the shaping of aluminum raw material into raw material by forcing it through a hole formed in a mold. After extrusion, the shape of the mold is applied throughout the aluminum. Aluminum extrusion can basically be likened to squeezing the toothpaste tube and taking the shape of the lid of the resulting paste..
Button TextAluminum Extrusion Process Steps. Aluminum extrusion profile production is a form of production which is difficult, laborious and multi-processed contrary to what it seems to be, although the increase in the number of firms in today's conditions seems simple due to increasing competition conditions and increasing competition. No part of the production does not accept the error and serious costs can arise in the slightest mistake. At any stage of our production, we are not afraid of high cost, we do not produce the products with the raw materials that do not have analysis that will put our customers in a difficult situation. For this reason, we earn happy customers by making 70% export and 90% of exports to European countries
1. Process raw materials as aluminum raw materials are called billets. Aluminum tickets are heated to 350 - 500 degrees Celsius. 2. After the billet reaches the desired temperature, the lubricant is transferred onto the film as a thin film. Heat will prevent the mold and the material from sticking together. 3. The billet is transferred to the carrier. 4. The billets are pushed in turn into the RAM enclosure. 5. Aluminum billets larger than the mold are in full contact with the carrier walls, crushed by the opposite mold. As aluminum is pushed through the mold, the liquid flows around the mold to cool the nitrogen process. In some cases nitrogen gas is used instead of liquid nitrogen. 6. The pressure finisher billet aluminum begins to squeeze out of the cavity of the mold. 7. The temperature is instantaneously measured and recorded during the extrusion process. The aim of knowing the temperature is to be able to maintain maximum pressure velocities. The target outlet temperature at the extruder also depends on the aluminum alloy. For example, for 6063, 6463, 6063A and 6101, the output temperature is at least 500 ° C 8. During profile drawing, the extrusion outlet is cooled by a series of fans along the length of the cooling table 9. On the billet block the oxidized part is discarded. 10. When the aluminum profile reaches the desired length, it is cut with the help of a profile saw. 11. The cut Aluminum Profile is transferred to the cooling compartment. 12. The aluminum profile is advanced, moved and cooled, then transferred to the next division, subjected to stretching and aligning operations (this part is important, there may be companies that do not do this in terms of cost and loss of work power). 13. The next step is the cutting saw. Aluminum profile is transferred to cutting saw and cut with certain length according to customer demand. 14. After the profiles are cut, they are placed in thermal baskets and transported into the furnace. Aluminum is hardened by aging (thermal treatment) in a controlled temperature environment. (This section is important, companies that do not do this in terms of cost and loss of work.) 15. Thermo-processed profiles shall be packaged and ready for delivery if no surface treatment (anodic coating, painting, wood transfer, etc.) or mechanical processing is to be done.
Button Text